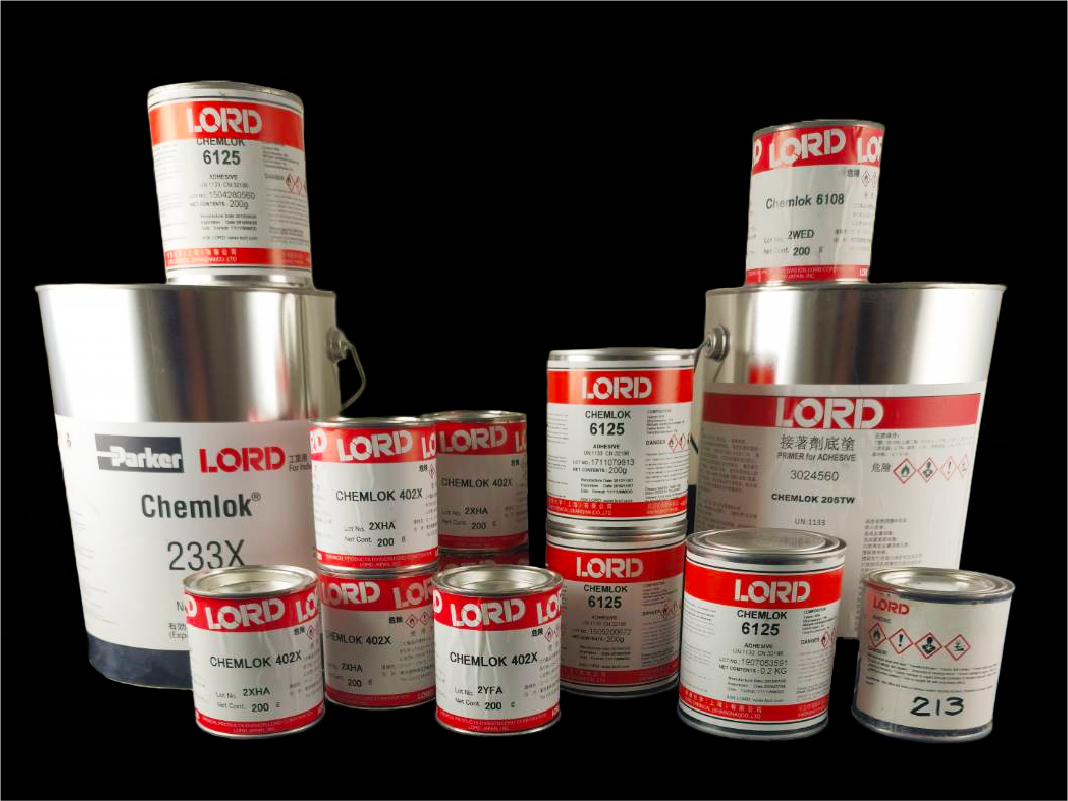
chemlok® ap-133 adhesive
Wide range of uses - good bonding performance, can bond various commercial mass-produced elastomers to many metal and non-metal substrates. Environmentally resistant - then strong. Withstands salt spray, chemicals, oils, solvents, corrosive gases and extreme temperatures. Strong durability - whether it is high temperature or low temperature, the adhesive strength provided is higher than the tear strength of rubber itself. Easy to Apply - Brush, Spray and Dip are all available.
Strong high temperature resistance - when it is bonded with fluoro rubber or silicone rubber, the highest temperature it can withstand is 204°C, and the lowest temperature is -51°C.
SURFACE PREPARATION - Thoroughly clean metal surfaces before applying adhesive. Use solvent-based degreasers or alkaline cleaners to remove protective oils, cutting oils and grease from metal surfaces. Choose appropriate chemical cleaning and mechanical cleaning methods to remove rust and oxide layers on metal surfaces.
- chemical cleaning
Chemical treatment can be used for metal parts that will be deformed during sandblasting or where the tolerance requirements are very strict. Phosphate is
The chemical treatment method is commonly used for steel, and the conversion coating method is usually used for aluminum.
- mechanical cleaning
Sandblasting is the most common method of mechanical cleaning. In addition, mechanical cleaning methods include steel brush cleaning, grinding or machining. Use steel grit to blast steel, cast iron or other ferrous metals. For stainless steel, aluminum, brass, zinc, and other non-ferrous metals use aluminum oxide, sand, or other non-ferrous metal grit.
Please carefully prepare the surface of non-metallic objects. Desizing treatment is usually required for textiles. Alkaline bath method can be used for glass, and solvent cleaning can be used for plastic surfaces. Wear clean gloves when cleaning metal surfaces to avoid contaminating the metal surface with oil from the skin.
Stir - Pour the adhesive into the bucket and dilute with toluene, methanol, or ethanol as needed. The average dilution ratio is 1:1 between adhesive and solvent, at this time the smallest amount of adhesive can provide the greatest adhesion and coverage.
The adhesive will evaporate quickly in a container with a large opening, so do not mix too much each time, and use it up as soon as possible after mixing. For porous substrates such as thick fabrics, in order to prevent excessive adhesion of adhesive on the substrate, a larger proportion of dilution may be required.
Application - Application of Chemlok AP-133 Adhesive should form a uniform film and can be applied by brushing, spraying or dipping. Adhesion strength may be reduced by repeated brushing or by mishandling when dipping and draining. When coating on textiles, according to the weight of the textiles, the adhesion amount of the adhesive after drying should be controlled at 0.05-1.0%. Spraying can effectively ensure that the adhesive adheres to the surface of the textile, and dilute the adhesive during dipping or spraying can prevent the textile from hardening due to excessive adhesion of the adhesive.
Drying/Curing - Air dry at room temperature for 10-30 minutes after application. Porous substrates may require longer drying times to ensure complete evaporation of solvents. The drying time should be extended when the humidity is high. Coated workpieces can be dried at high temperature, drying at 104°C (220°F) for 15 minutes to obtain excellent adhesion properties. The workpiece coated with adhesive can be bonded immediately after natural air drying. If it needs to be placed for a long time before bonding, the workpiece coated with adhesive should be avoided from being polluted during storage. Adhesive-coated parts can be stored for up to three days before bonding, but if humidity is high, the storage time can be significantly shortened.
For each elastomer, use the manufacturer's recommended curing temperature and time. In many cases, secondary vulcanization improves bond strength. If the lowest recommended temperature is used and the heat cure time is too short, poor adhesion may result. Removal of the cured object from the mold requires caution. Good adhesion is obtained with Chemlok AP-133 using steam cure, autoclave cure, and other cure methods. There needs to be full contact between the rubber and the mating surface.
Drying or secondary vulcanization treatment can improve the bonding strength, because the curing temperature and time exceed the molding curing conditions. Gradually increase the secondary vulcanization temperature in order to diffuse the volatile material and stabilize the physical properties. Post-cure starts at 10°C below molding temperature and increases gradually to the highest end-use temperature over 2 to 3 hours.
The following parts need to be subjected to a temperature adjustment procedure at a lower temperature, and must not be exposed to high temperatures before that. If the end use temperature exceeds 204°C, temperature programming is a very important step. Corrosion of metal parts at high temperatures will reduce the bonding strength. Especially if the metal parts are contaminated or the surface treatment is insufficient. ChemlokAP-133 can withstand many harsh environments, and electroplating or anodizing the metal after the bonding will not damage the bonding.
The shelf life is one year after shipment from the production factory, stored in the unopened original packaging in a ventilated environment at 21-27°C. Do not store or use near heat, sparks or open flames.
- Precautions
Before using this or any LORD product, please refer to the Safety Data Sheet (SDS) and product label for safe use instructions. For industrial/commercial use only. Those who use this product must undergo relevant training in advance. Not for domestic use. Not for use in consumer products.